A Brief History of Building Facade Sealant Repair
Before the 1950’s building façade sealants did not exist. Building joints were sealed with oil based caulks, which provided protection from the effect of weathering. The development of new sealant technology and flexible rubber sealants opened the door to non-masonry, high thermal movement building exteriors (like aluminum), and façade curtainwall (curtainwalls are defined as nonload bearing walls that are attached to floor lines and columns only) construction.
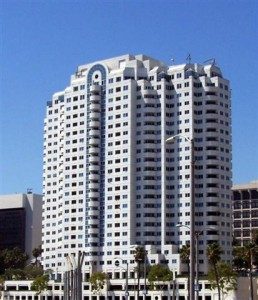
These lightweight walls heat and cool rapidly thus creating a high stress environment which will take its toll on exterior building sealants. The characteristically high movement in curtainwall structures makes it necessary to design appropriate joints and use a sealant with good movement capability.
The first sealants were based on polysulphide polymers. They were followed by acrylic, silicone and polyurethane sealants. Each has its own unique properties causing them to perform differently under varying conditions. The differing strengths and weaknesses demand varying surface preparation techniques and uses. A thorough understanding of all these materials by the sealant contractor is necessary to ensure that the most effective sealant is specified for and applied to a particular project.
Building Facade Sealant Repairs & Replacements
Since sealants do not have an indefinite life span, they eventually need to be replaced. Prior to actual replacement it is important to determine what happened to require replacement. If joint failure has occurred, the cause should be determined to prevent a reoccurrence of the problem.
There are four basic types of joint failure:
- Adhesive failure- The sealant has separated cleanly from the surface of the substrate.
- Cohesive failure- When a sealant tears within itself, it has failed cohesively.
- Substrate failure- When the substrate material ruptures or delaminates at or below the bond line.
- Loss of Sealant Properties- The useful life of a sealant is dependent upon the quality of the workmanship during installation and the actual sealant properties as compared to the manufacturers written statements.
There are two common approaches to joint sealant restoration: complete removal and replacement or use of a “bridge joint”. Complete removal is defined as the removal of all traces of sealant, because any remaining sealant could deter proper adhesion of the new sealant. An overlay joint repair or “bridge joint” allows the new sealant to bridge over the existing sealant from the face of one side of the joint to the other without adhering in the center.
A good façade inspection program helps the Owner establish the need for maintenance, identify the cause of the problems, and prescribe appropriate maintenance and repair procedures. Regularly scheduled inspections of structures can detect small problems before they cause damage and require costly repairs.
Once the problems are found or located and the Owner recognizes there are problems, the Owner can either hire an Architect or go to a Specialty Contractor for their recommendation for repair. The Architect/Engineer or Specialty Contractor should base their recommendations on the industry’s latest standard of repair methods for each type of repair that must be made to the building.
Prior to preparing the specifications for the performance of the work, it is necessary to determine from the types of repairs that are to be made the performance level of the material that will be needed. Once the performance level has been recognized and measured, if possible, then the selection of the proper material to meet these requirements can be made.
The Architect/Engineer can readily prepare specifications for a competitive bidding process or solely for negotiated uses; usually on a fee basis. Certain Consultants or Specialty Contractors are also capable of providing these specifications sometimes on a fee basis or as part of a negotiated or design-build project.
Once a specification has been completely prepared and a Contractor has been chosen and contracted, the actual performance of the work takes place. Both during and at the end of the project the Owner/Owner’s Agent is ultimately responsible for the approval or non–acceptance of completed work items.
Curtis Murrell has 25 years experience as a General Contractor specializing in high rise waterproofing and is the current Vice President of PCW Contracting Services, Costa Mesa, CA. Contact: Curtism@pcwservices.com
Robert Hill has over 25 years experience as a waterproofing and restoration specialty Contractor/Consultant and is currently employed with Angelus Waterproofing and Restoration, Inc. Huntington Beach, CA. Contact: RobH@angelusWP.com