To repair now or to repair later is the age-old dilemma associated with owning or managing a building or community. Sticker shock from contractors is all too common when it comes to receiving a proposal for any type of maintenance or repair work. The goal should be, however, to keep the sticker shock from turning into a sticker heart attack. A sticker heart attack can occur when maintenance is deferred and pushed down the road too far to the point when the only possible cure is a complete replacement of the building assembly. At that point, there is no other alternative to prevent additional costly repairs than to tear out the assembly and start all over again. The most common culprit for causing this damage is water. Water has a bad habit of finding any opening within an assembly, entering that opening, and spreading out from there. Untreated water damage of a building is one of the many reasons for board of directors to experience a sticker heart attack.
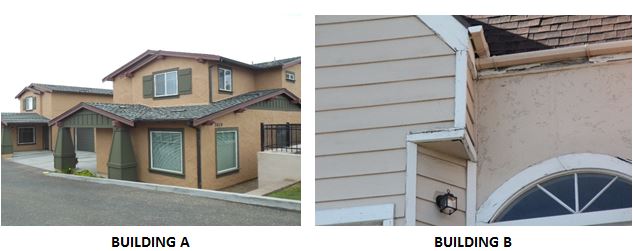
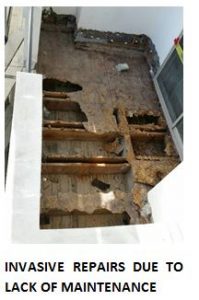
Let’s take a look at two different buildings and the result of performing routine maintenance and deferring maintenance. In the photos above, building “A” has undergone periodic maintenance to keep the wood trim sealed and water tight. There may be some areas where paint is peeling or flaking, but the overall condition of the materials are in good shape. The cost to make the minor repairs and apply a new coat of paint, while expensive, is certainly within budget. Building “B” has not undergone periodic maintenance; instead no maintenance has occurred for many years. The paint and sealant has failed and peeling off, exposing the raw wood to the elements. The lack of useful paint and sealant allows water to penetrate the wood and start the deterioration process. Since no work has occurred for some time, the wood has started deteriorating. The costs involved with making these repairs are much more significant; not only does the deteriorated wood itself need to be replaced, but the surrounding stucco needs to be removed in order to replace the wood. The size and scope of the repair for building “B” has doubled or tripled in size compared to building “A.” The cost for repairing building “B” could not only result in a sticker heart attack for the board of directors, but also for the residents of the community when they receive the unexpected special assessment letter in the mail.
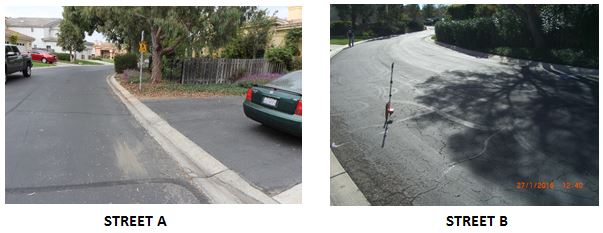
When it comes to maintenance, most people think about the exterior and interior components of a building. Few people think about the community streets they drive or the planters they look at. These components also require routine maintenance in order to achieve the maximum useful life of the system. Let’s compare another two photographs to see what the result can be if routine maintenance is performed.
In the photos above, street “A” has some minor cracking in the asphalt, but nothing appears to be too major. Street “B” on the other hand has large cracks crisscrossing the asphalt, in a pattern commonly referred to as “alligator cracking.” Alligator cracking is the result of water seeping through cracks in the asphalt, saturating the underlying material (known as base), resulting in the asphalt moving more than it was designed to move.
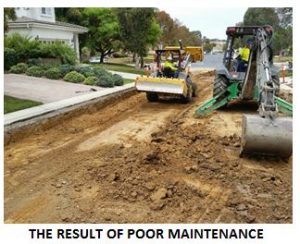
If caught soon enough, like in Street “A”, the crack can be filled with a tar-like material and the entire street can be covered with a “slurry seal” that will protect the asphalt from water seepage and maintain the elasticity of the asphalt. The result of Street “B”, however, will be a full removal and replacement of the asphalt and base material (as can be seen in the adjacent photograph), providing another source of sticker heart attack for the board of directors and source of inconvenience for the residents when they cannot access their driveways for days at a time due to the streets being torn up.
There are many more examples of good maintenance habits and poor maintenance habits that can be reviewed. However, the most important thing to remember when owning or managing a building or community is that a little bit of sticker shock now can save the pain of a larger sticker heart attack later.
Elliott Meier, Project Manager at Bethco Builders, www.BethcoBuilders.com
With a degree in Construction Management from Cal Poly San Luis Obispo, Elliott is an important team member at Bethco Builders and to our clients. Since his 2009 graduation, he has gained valuable experience managing and estimating residential and sit improvement projects. Elliott is adept at managing multiple projects simultaneously. His technical skills include Xactimate 27.5, SketchUp, AutoCAD, Primavera, and a variety of Adobe and Microsoft Office applications. Elliott is OSHA certified, Council-certified Microbial Remediator (CMR), and Lead RRP certified.